LCA4Sim
Life cycle assessment in plastic injection moulding simulationAbout the project
This German research project has the long-term goal of enabling the prediction, measurement and optimization of the environmental footprint during the design of plastic manufacturing and building components. The project aims to integrate this functionality directly into the simulation software CADMOULD for plastic injection molding. Such functionality will enable engineers to make optimizations under the consideration of sustainability predictively rather than retrospectively, as has been the norm previously.
The key outcome will be to establish interoperability between SIMCON’s plastic injection molding simulation software CADMOULD and GreenDelta’s life cycle assessment software openLCA. This will enable plastics engineers to predict and optimize the ecological footprint of their material choice, as well as their part and mold engineering decisions, in plastic injection molding. Technically, this will necessitate a mapping between plastic injection molding and external life cycle assessment data.
GreenDelta in the project
GreenDelta will be involved in two of the key aspects of the project. The first will be to identify what external data from life cycle assessment databases can be integrated with existing plastic injection molding data so that environmental impacts can be predicted quantitatively. The second aspect will be to work with SIMCON to craft a suitable interface between openLCA and CADMOULD.
Partners
The parties working on this project are:
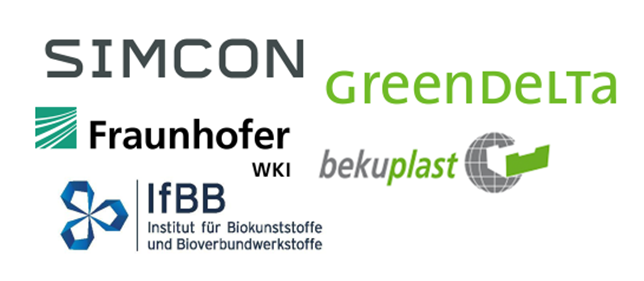
- SIMCON kunststofftechnische Software GmbH
- GreenDelta GmbH
- bekuplast GmbH
- Fraunhofer-Institut für Holzforschung, Wilhelm-Klauditz Institut WKI, Anwendungszentrum HOFZET®
- IfBB, Hochschule Hannover
Background
Plastics are used in a wide variety of products ranging from packaging to components of electronics, household items, furniture and vehicles. Due to their light weight, their unique functional qualities, the wide variety of shapes it can be cast into, and their relatively low energy intensity in mass production (compared to alternatives like metals), plastics are likely to remain indispensable materials well into the future.
However, in recent years, the use of plastics has been discussed critically in the public discourse. Since the production of plastics is presently largely dependent on hydrocarbons, the carbon footprint of plastics has come under scrutiny. Additionally, plastics pollution of the oceans (particularly from product packaging) poses a threat for marine life. This is exacerbated by the fact that many plastics today are not yet being recycled.
For cases where plastics are the best available material, the question thus becomes which plastics to use and how to use them. Clearly, sustainability aspects must be considered in the design, production and use of plastics. Different plastic material classes should be compared not only in terms of their technical suitability, but also in terms of their ecological footprint. Functional needs, cost targets and sustainability requirements must be met simultaneously, necessitating new kinds of designs.
To develop such designs, it is a good idea to use simulation to explore a wide range of options, rather than relying exclusively on real-world experiments. However, while engineering simulation software can already help with cost and functional assessment, the ecological footprint is not yet integrated in the same systems.
Life cycle assessments (LCA) are a way to predict and quantify ecological footprints. They can be used to comparethe sustainability footprints of several different materials, to arrive at more well-informed materials decisions and manufacturing processes. To have an impact on product design, this quantification needs to be predictive – i.e. engineers need the quantification before final decisions have been made about materials, part and process design. A retrospective “stock taking” would be too late, because by then, all major design decisions will have already been made, and high costs have already arisen. For this kind of predictive LCA to be practical in reality, it needs to be as accurate, simple and effortless as possible.
This project is about linking LCA assessment with injection molding simulation in a way that enables better all-things-considered engineering decisions, co-optimizing sustainability, functional and cost considerations.
Project sponsor: Forschungszentrum Jülich GmbH
Project funded by BMBF
Project duration: 2022 – 2024
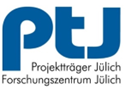
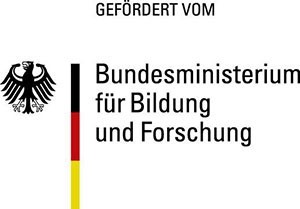